Game Manufacturing 101: From Concept to reality
- Kim Drayer, EPI/Delano Service
- Nov 17, 2015
- 6 min read

So, you’re sitting down with friends or family to play a board or card game. Have you ever stopped and wondered: how was this game made? Well, we know. We bring games to life/reality and LOVE what we do. Here at DeLano Service, a division of EPI Marketing Services, we’ve been producing games domestically for over 30 years, from the basic card game to complex board games (everything except plastic/wood pieces). To give you a better idea of how games are made, let’s walk through the production process of a simple board game.
Most board games consist of a 2-piece box, platform, game board, card decks, rules, game pieces (dice, pawns, die cut tokens, sand timer, etc.) and then packing/assembly of the game. Games can have any combination of these components, depending on what the creator wants — more complex games can include card trays, tuckboxes for the card decks, game stands, score sheets, money, spinner board/arrows, etc. The whole process begins with the game creator, the person or company looking to manufacture a game. All games begin the same way, however: with the concept. When a game creator decides that a game is ready to print, they work with a manufacturer like us to receive guidance, recommendations, support, and pricing estimates before beginning the actual printing process.
Let’s assume all the elements of the game have been determined and it’s time to move forward with production.
There are 3 main phases to the production process:
Phase 1: Prepress
The game creator submits all the artwork files and some really creative people will take the files and make sure all the artwork “fits” on the appropriate sized paper. They create the die lines and layouts that will be used during production for each printed component, ensure any cards are laid out in the preferred order, and place the front and back sides of each card as required. When this is completed, the proofs are sent back to the game creator, who must review and sign off on the design. This is the approval to move forward with the game production. This process can vary with the amount of time required, as it depends upon the number of revisions that are needed; however, once the approval is received, it’s time to bring the game to life, which usually requires 4-6 weeks (more during the peak holiday season).
Phase 2: Press and Post Press of Individual Components
The game artwork needs to be printed, whether it’s the artwork for the lid (box top) or base (box bottom), the game board, cards, rules, etc. Each component can be run on one of several presses and will go through multiple finishing operations after it has been printed to become the final pieces going into the game. These components will later be “married up” at the game packing/assembly stations.
The Package (2-piece setup box):

EMMECI BOX MAKER
Most board games are contained in a setup box, meaning a box that has a lid and a base (box top/box bottom). For a setup box, the core of the box that provides the strength is a piece of 32 or 40 point (pt.) chipboard that has been scored and cut out into a shape that resembles a cross. It is then formed on a Box Maker, reinforced on the corners with tape, and wrapped with a sheet of printed paper to make the finished box top or box bottom.
Platform:
Most game creators like to include a “platform” in the game, which is designed to hold the game components for safe keeping while the game is being stored or transported. These can be manufactured using either corrugated e-flute material or plastic injection molding. E-flute material is much like what a standard shipping carton is made of, only in this case it is die cut (a process by which shapes are made using the manufacturing equivalent of a cookie cutter) to resemble a tray to compartmentalize the components. Plastic injection-molded inserts are custom-fitted plastic forms to hold the components more securely, and are typically used in more complex games with lots of components. However, they are significantly more costly because molds need to be created.
Game Board:

EMMECI RIGID BOARD MAKER
A game board is generally 79 pt. chipboard, which provides a lot of strength. The board is wrapped on both the outside and inside with sheets of paper. Often, it’s just a printed sheet on the inside and a plain black (textured/bubble-like) material that is very durable on the outside — however, printed sheets can be used for both sides of the board. They are produced on a Board Maker and finished by being die cut with slits and scores that allow the end user to fold them down. Game boards can be no-fold boards, bi-fold, tri-fold, quad fold and 6 panel boards. Most game boards are bi-fold and quad fold.
Cards:
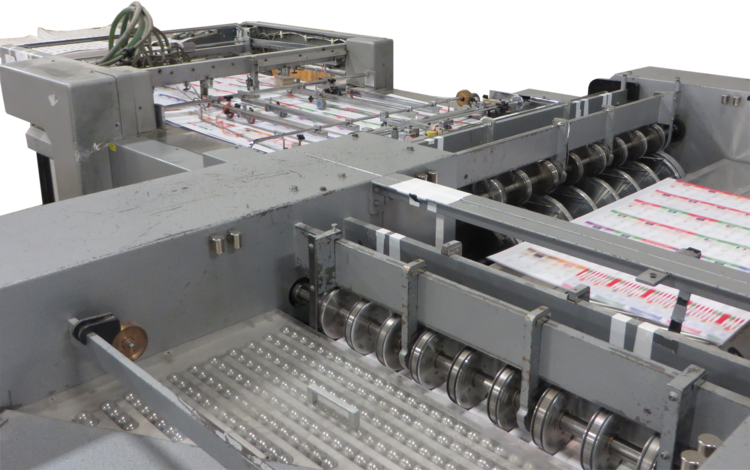
ROLLEM SLIPSTREAM COLLATOR
Most games contain some quantity of cards. There are a variety of papers that can be utilized depending upon how frequently cards are shuffled, what age the player is, etc. Cards can be a multitude of sizes (mini, standard poker, bridge, flash card, etc.) and are printed on both sides and then collated (gathered) via mechanical means. There are 2 ways to collate cards, and the number of cards in the deck really dictates which method is used. Rollem Slipstream collators are used to collate full sheets of cards. The sheet is fed into the Rollem unit and slit in one direction; it is then turned 90 degrees and fed into a second set of slitters to divide the cards into individual pieces. They continue on through the machine, where they are collated down into a single deck and ejected out of the machine. The print layout (submitted/approved during the prepress stage) is what determines the order, so cards can be laid out to print multiple cards on a sheet of paper and collate down to be A, B, C, D, etc.
The second method of collating cards is via a collator sheet. Cards can be printed in multiples of the same card or a specific set of cards, then trimmed down into sheets designed to be stacked to complete the collation. They are then trimmed down to the final size and stacked on top of each other (merged) to form the final deck.
Cards can be inserted in a tuckbox — in this type of box, the top and/or bottom of the box is folded or tucked; the bottom can also be glued shut. Some tuckboxes include a hang tab for easy display in retailer locations. Most cards included in a game are typically shrink-wrapped (wrapped and heat sealed in plastic) or they are fin-sealed, whereby the top and bottom of the plastic is pressed together to create a seal and the packaging is loose (not tight-fitting like shrink wrap). For some games, cards are bound together with rubber bands.
Rules:
Players need to know how to play the game, right? There are variations on how to produce the rulebook. For simpler games, rules can be printed on a thin, white sheet of paper and folded down to size or stapled (saddle stitch) into 4 or more pages and included in the game. More complex games with in-depth rules that require pictures and expanded explanations are manufactured as stitched booklets. Often, these are printed in full color on a glossier paper stock. Less frequently, the rules are printed on the box itself — the box bottom or on the inside of the box top (lid).
Game Pieces:
Dice, pawns, tiddlywinks, tokens, etc., are also very frequently found and used in games. Tokens, for example, can be manufactured by either printing 2 sheets of heavier board stock and mounting them together, or printing litho sheets that are then mounted to chipboard to give the game pieces more strength in the core. In both cases, these are then die cut (remember the cookie cutter as described previously) into individual playing pieces with any shape the game creator chooses. Other items, such as custom molded plastic pieces and wooden components, are sourced from factories that specialize in these materials. Often, these factories are located overseas, as it is still quite cost prohibitive to obtain plastics and wood components domestically.
Phase 3: Packing and Assembly
During the manufacturing process, the various game components are produced on many different pieces of equipment, in various locations in the production facility. Packing and Assembly is the process where all the components are “married up.” First, a single game is put together and approved as the master. Subsequent games are assembled the exact same way and quality checked to the master frequently. The assembly/packing lines (with additional components placed behind the lines to continuously supply the assemblers/packers) consist of actual human beings putting the games together. The empty box bottom is placed on a moving belt and as it moves down the line the specified components are placed inside. As the final step, the lid is placed over the top and the games are shrink-wrapped in plastic for display at a retail store. They are carton packed and stacked on pallets for shipment or storage.
Now that you know a little bit more about how your favorite games are made, go PLAY and have FUN!
This article was originally published in the Summer 2015 issue of Casual Game Insider magazine.